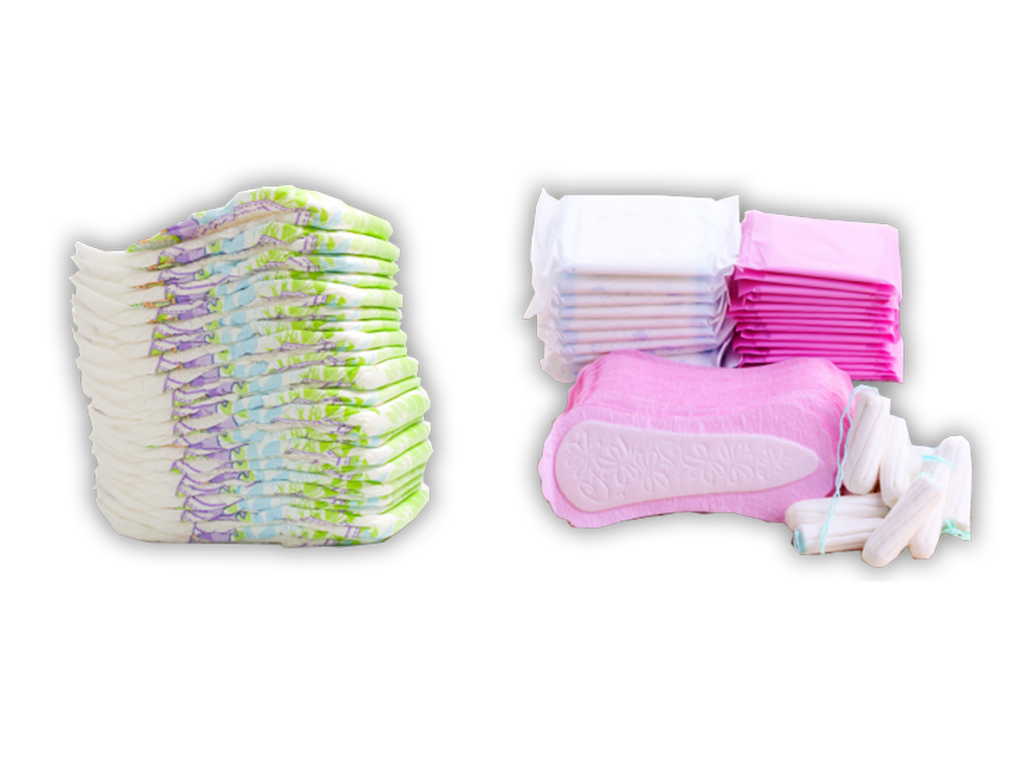
If you’re buying diapers or feminine care products, you want the assurance that those items weren’t handled by hand during the manufacturing process. Knowing that, companies have automated their processes upstream to remove the human touch element during manufacturing.
However, that’s not necessarily the case downstream at the end of the line when packing product into cases, and it’s easy to understand why. When products are ready to be packed into cases, they’ve likely already been packaged and wrapped, so there’s less concern about people handling them. This may be why some smaller to midsize companies still hand-pack products, which is a perfectly acceptable practice and one that they’ve done successfully for years.
But could they be doing it more efficiently and saving money in the long run by automating their case packing? Yes they could, and here’s why.
Automation gains you efficiency. It’s common for some companies to go and hire 20 or more temporary workers when needed to pack a big shipment. On a slower production day, they may only need 10. This strategy of ramping up only when needed can limit your growth in not being able to adequately meet large increases in volume. While time is being spent, trying to hire and manage a large group of temporary workers you also have to factor in the cost and insurance for having those workers onsite.
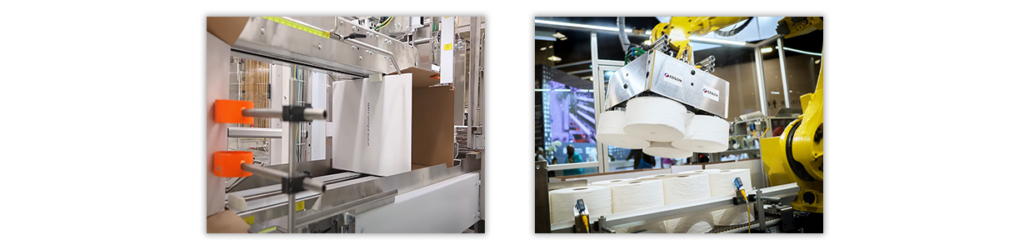
Another reason for automating is rooted in lessons learned from the COVID-19 pandemic. Most manufacturing companies have allocated extra space among employees for social distancing, and some of these added safety measures may be permanent fixtures moving forward. This can pose a problem if your line is staffed with 20 or more during your busy periods. Automating your case packing operation greatly minimizes social distancing concerns by reducing staff operating those lines.
Additionally, if you are hand-packing product, you probably have not automated your palletizing operation either. This means you have people building and stretch wrapping pallets. Repeatedly bending over or twisting to hand wrap pallets can lead to painful back strain injuries; that employee is now off the job and costing you money in lost production, medical bills and workers compensation claims.
Automation is truly driving case packing for not only diapers and feminine care products, but other converted paper products like toilet paper, paper towel, tissue and other items. Machinery today is flexible enough to handle a variety of sizes with quick, easy-to-initiate changeovers thanks to intelligent HMI interface. In the packaging process, you never want to be the bottleneck that backs everything up. By automating your case packing process, those fears are gone.
There’s a reason why most major converted paper expansion within North America in the past several years has used Edson for their end-of-line case packing. Are you next?
Leave a Reply